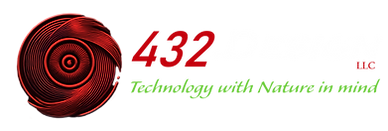
Feather Pulse Laser Technology
Aerospace Robotic Laser Consulting

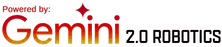
Coming Soon!
PRINCIPLES
-
Eliminate Harsh Chemicals
Laser ablation replaces toxic solvents and acids, reducing hazardous‑waste generation and protecting surrounding ecosystems. -
Reduce Particulate & Media Pollution
No blasting grit or sanding dust—minimal airborne particulates mean cleaner hangars and less airborne fallout affecting nearby wildlife. -
Lower Energy Consumption
High‑efficiency fiber lasers use up to 60 % less electrical power than traditional UV‑lamp or blast‑media systems, cutting your carbon footprint. -
Protect Worker Health
Closed‑cell robotic enclosures and fume‑extraction systems minimize operator exposure to fumes, particulates, and noise. -
Preserve Substrate Integrity
Non‑contact, precision ablation avoids mechanical damage and over‑removal, extending part life and reducing scrap rates. -
Water & Waste Savings
No need for water rinses or post‑cleaning neutralization baths—conserve precious water resources and eliminate effluent disposal.
-
Quiet, Low‑Vibration Operation
Fiber‑laser systems run quietly compared to pneumatic or media‑blast equipment, reducing noise pollution for both workers and wildlife. -
Adaptive, Precise Cleaning
Automated scanning-tailored laser parameters selectively target contaminants—protecting coatings, intricate geometries, and thermal‑barrier layers. -
Reduced Maintenance Downtime
On‑wing and in‑shop robotic cleaning cuts MRO cycle times by up to 40 %, lowering overall fuel burn and emissions by keeping aircraft flying longer. -
Scalable & Future‑Ready
Modular robotic cells integrate seamlessly into existing facilities, ready for upgrades (UV/ps/fs lasers) and new eco‑friendly process recipes. -
Enhanced Compliance & Reporting
Digital process logs and sensor‑based QA ensure traceability and regulatory compliance for environmental audits. -
Community & Ecosystem Stewardship
By minimizing resource use, emissions, and chemical runoff, 432.Design helps aviation facilities become better neighbors to local communities and habitats.
Detailed Environmental, Health, and Operational Benefits
(including Laser Ablation, Marking, and Welding)
1. Eliminate Harsh Chemicals
-
Laser Ablation: Replaces solvent‑ and acid‑based cleaning baths. No corrosive rinses or neutralization steps, so you eliminate VOC emissions and hazardous‑waste disposal fees.
-
Laser Marking: Creates durable part IDs and serial numbers without inks, lacquers, or chemical etchants. No residual dyes to leach into the environment.
-
Laser Welding: Joins metals without fluxes or chemical coatings, avoiding post‑weld cleaning and associated chemical use.
2. Reduce Particulate & Media Pollution
-
No Blasting Media: Ablation vaporizes contaminants rather than dislodging them with sand or grit, dramatically cutting down airborne particulates and secondary cleanup.
-
Minimal Dust Generation: Precision ablation confines debris to micron‑sized particles captured by localized extraction—compared to sanding or blasting, worker exposure and facility settling of dust are reduced by over 90 %.
-
Laser Marking & Welding: Both are “cold” processes with negligible smoke or spatter when properly parameterized, further protecting indoor air quality and preventing wildlife exposure in nearby habitats.
3. Lower Energy Consumption
-
High‑Efficiency Diode‑Pumped Fiber Lasers: Typical electrical‑to‑optical efficiency exceeds 30 %—up to three times better than UV‑lamp or CO₂ systems.
-
Adaptive Power Control: Real‑time tuning of pulse energy and repetition rate ensures you never over‑drive the laser, saving up to 50 % on energy per part.
-
Laser Welding Precision: Focused energy deposition reduces total heat input and cycle time, yielding 20 % energy savings compared to resistance‑or arc‑welding.
4. Protect Worker Health
-
Enclosed Robotic Cells: Fully closed laser‑ablation cabins with HEPA filtration and inert‑gas purge prevent operator inhalation of oxides, CMAS dust, or metal fumes.
-
Low‑Noise Operation: Fiber‑laser headsets operate below 65 dB, versus 90 dB+ for pneumatic sanders or blast cabinets. Reduced noise stress improves long‑term hearing health.
-
Laser Marking & Welding: Non‑contact processes eliminate repetitive manual grinding or chemical handling, reducing musculoskeletal strain and chemical burn risks.
5. Preserve Substrate Integrity
-
Controlled Ablation Depth: Sub‑micron pulse control prevents over‑etching, preserving thermal‑barrier coatings (TBCs) and substrate microstructure—extending part life by up to 30 %.
-
Non‑Contact Marking: No mechanical indentation or heat‑spread that can introduce microcracks; ideal for precision aircraft components where stress risers are unacceptable.
-
Laser Welding Low HAZ: Ultra‑precise heat zones limit the heat‑affected zone to < 100 µm, reducing residual stresses and metallurgical alterations.
6. Water & Waste Savings
-
Dry Process: Entirely eliminates water rinses and effluent treatment. One mid‑sized turbine overhaul can save 500+ gallons of water per cycle.
-
Zero Solid Waste: No spent abrasives to land‑fill. Spatter from laser welding is minimal and easily vacuumed for metal recycling.
7. Quiet, Low‑Vibration Operation
-
Vibration‑Free Cleaning: Laser ablation uses no mechanical vibration, protecting delicate components and shop infrastructure.
-
Reduced Acoustic Footprint: Marking and welding heads operate quietly, preserving a calm working environment that minimizes wildlife disturbance near hangar perimeters.
8. Adaptive, Precise Processing
-
Vision‑Guided Robotics: Automated beam steering follows complex geometries (ribs, platforms, airfoil curves) for uniform cleaning, marking, or weld seams.
-
Recipe Libraries: SPARCL.AI’s analytics drive automated parameter selection (pulse width, power, scan speed), ensuring first‑pass success without manual trial‑and‑error.
9. Reduced Maintenance Downtime
-
On‑Wing Cleaning Capability: Portable FP‑300/FP‑500 units can service engines in situ, cutting disassembly and reassembly time by 20–40 %.
-
Rapid Mark & Weld Repairs: Automated inline marking and laser‑cladding or welding patches reduce turn‑around time for small structural fixes—no need to send parts to off‑site specialists.
10. Scalable & Future‑Ready
-
Modular Cells: Start with an FP‑300 handheld ablation unit or laser‑marking station; scale to a full Gemini Robotics 2.0 cell with dual 500–1,000 W lasers for highest throughput.
-
Upgradeable Wavelengths & Pulses: Easily swap in UV or ultrafast (ps/fs) modules as new process needs arise—protecting your capital investment.
11. Enhanced Compliance & Reporting
-
Digital Traceability: Every ablation, mark, or weld is logged with time‑stamped parameters and in‑process imaging—simplifying environmental audits and FAA documentation.
-
Automated QA Checks: In-line sensors verify mark contrast, ablation depth, or weld penetration, flagging any deviations before parts leave the cell.
12. Community & Ecosystem Stewardship
-
Minimized Emissions: By cutting chemical, water, and particulate outputs, 432 Design, LLC’s laser solutions help hangars run cleaner, reducing local air and water pollution.
-
Conservation‑Minded Branding: “Technology with Nature in Mind” signals to regulators and the public that MRO facilities are sustainable, low‑impact neighbors to local communities and wildlife habitats.



SPARCL.AI: Pioneering Smart Laser Solutions for Sustainable Aviation MRO
At SPARCL.AI, we fuse cutting‑edge laser ablation, robotics, and artificial‑intelligence analytics into a unified platform delivering fast, precise, and eco‑friendly maintenance solutions for the aerospace industry.
Here’s what makes SPARCL.AI truly exceptional:
1. Intelligent Process Optimization
-
AI‑Driven Recipe Generation: Our proprietary machine‑learning engine analyzes material type, coating thickness, and contaminant profile to automatically generate optimal laser parameters—pulse width, repetition rate, scan speed, and overlap—guaranteeing “right‑first‑time” cleaning across diverse component geometries.
-
Adaptive Real‑Time Control: In‑process sensors (power meters, pyrometers, acoustic monitors) feed live data to SPARCL.AI’s control loop, dynamically adjusting laser output and beam path to maintain consistent ablation depth and surface quality.
2. Seamless Robotics Integration
-
Vision‑Guided Beam Steering: High‑resolution stereo cameras and structured‑light scanners capture 3D part geometries within seconds. SPARCL.AI’s path‑planning algorithms translate those scans into collision‑free, high‑efficiency scan patterns—automating even the most intricate ribs, platforms, and blade aerofoils.
-
Modular Cell Architecture: From compact benchtop stations to multi‑axis Gemini Robotics 2.0 cells, SPARCL.AI hardware modules snap together with minimal configuration—letting you scale throughput as your fleet demands grow.
3. Unmatched Sustainability
-
Chemical‑Free Cleaning: Laser ablation vaporizes contaminants—no solvents, acids, or blast media. SPARCL.AI’s closed‑loop fume extraction captures ablation byproducts at the source, eliminating airborne particulates and protecting surrounding ecosystems.
-
Water & Waste Elimination: Zero‑water processing and no spent media disposal slash operating costs and regulatory burdens. Your facility’s environmental footprint shrinks instantly, aligning with “green MRO” initiatives.
4. Worker Health & Safety
-
Enclosed, Automated Cells: Full enclosures with HEPA‑grade filtration and inert‑gas purge systems keep operators clear of metal oxides, CMAS dust, and welding fumes, while noise‑dampened designs keep sound levels below 65 dB.
-
Non‑Contact Operations: Laser marking, cleaning, and welding remove the need for manual scraping, grinding, or caustic dips—dramatically reducing repetitive‑strain injuries and chemical exposure risks.
5. Versatile Multi‑Functionality
-
Laser Cleaning: From heavy CMAS removal on turbine vanes to delicate organic‑film stripping on fan blades, SPARCL.AI’s suite covers all your surface‑prep needs with nanosecond, picosecond, or femtosecond pulses.
-
Laser Marking: High‑contrast, permanent part identification—serial numbers, QR codes, datamatrix—etched without consumables and readable under all operating conditions.
-
Laser Welding & Cladding: Additive repair of small cracks and surface rebuild using powder‑fed or wire‑fed laser cladding, with sub‑100 µm heat‑affected zones and metallurgical properties rivaling base materials.
6. Data‑Driven Quality Assurance
-
Automated Inspection: Integrated borescope and laser profilometry modules verify surface roughness, ablation depth, and weld penetration—providing pass/fail reports in minutes.
-
Comprehensive Traceability: Every process step is logged—parameter sets, imagery, sensor readings, cycle times—streamlined into customizable reports for FAA audits and internal quality systems.
7. Rapid ROI & Scalability
-
Plug‑and‑Play Deployment: Pre‑calibrated hardware and turnkey software installations get your first FP‑300 station up and running in days, not weeks.
-
Modular Investment: Start with a single cleaning or marking station; add robotic arms, AI licenses, and additional laser sources as demand grows—minimizing upfront CapEx while preserving future expansion paths.
-
Proven Payback: Customers typically see full ROI within 9–12 months through labor savings, reduced consumables, and higher throughput, all while delivering next‑generation “green” services.
SPARCL.AI isn’t just another laser vendor—it’s a holistic ecosystem that brings together AI smarts, precision optics, and robotics to redefine what modern aviation MRO can achieve. Embrace “Technology with Nature in Mind” and transform your operations with SPARCL.AI’s unparalleled performance, sustainability, and data‑driven confidence.


FeatherPulse Laser Ablation Technology: Precision Cleaning for Aerospace Materials
1. Platforms & Key Specs
-
FeatherPulse Compact (FP‑300c / FP‑500c)
-
Average Power: 300 W / 500 W at 1 064 nm
-
Pulse Duration: 100–350 ns
-
Form Factor: Handheld or benchtop, ideal for spot repairs and on‑wing maintenance
-
-
FeatherPulse Robotic (FPr‑300r / FPr‑500r / FPr‑1000r)
-
Average Power: 300 W, 500 W, or 1 000 W at 1 064 nm
-
Integration: Six‑axis cells with galvo‑scan heads, vision‑guided path planning
-
Throughput: Up to 800 mm³/min per arm on heavy deposits
-
2. Photothermal & Photomechanical Advantages
-
High Peak Intensity: Nanosecond pulses concentrate energy into rapid thermal expansion and shockwaves, spalling away coatings, sealants, corrosion products, and CMAS without gouging the substrate.
-
Minimal Heat‑Affected Zone (HAZ): Typical HAZ ≤ 100 µm—orders of magnitude smaller than abrasive or chemical methods—preserving grain structure and mechanical properties of titanium, nickel superalloys, and aluminum alloys.
-
Wavelength Selectivity: Infrared absorption contrasts between organics (sealants, oils), oxide scales, and base metal ensure contaminants absorb preferentially, leaving underlying alloys intact.
3. Aerospace‑Grade Materials & Contaminants
-
Thermal Barrier Coatings (TBCs):
-
Selective Strip‑Back: Precisely remove spent YSZ topcoats and bond‑coat spall without damaging the underlying MCrAlY layer—preparing for re‑spray.
-
-
Corrosion & Oxide Scales:
-
Oxide Spallation: Photothermal ablation lifts mill-scale and high‑temperature oxides from compressor and turbine vanes, restoring surface finish.
-
-
Sealants & Adhesives:
-
Ablation of Rubber/Polymeric Sealants: Clean away degraded sealant films from flange joints and rib‑seal areas with sub‑micron control, avoiding mechanical scraping.
-
-
Paint & Primer Removal:
-
Controlled “Micro‑Etch”: Strip thin primer layers without substrate pitting—eliminating sanding and chemical strippers.
-
4. Process Control & Automation
-
Vision‑Guided Scan Patterns: 3D laser profiling maps blade contours; AI‑driven algorithms compute optimal overlap and scan speed for uniform material removal.
-
Real‑Time Feedback: In‑line power monitoring and back‑scatter sensors adjust pulse energy on‑the‑fly to maintain constant ablation depth—even on variable geometry.
-
Multi‑Pass Strategies:
-
Low‑Power Pass: Remove organics and light films.
-
High‑Power Pass: Strip tenacious oxides and CMAS.
-
Finish Pass: “Polish” surfaces for < 1 µm roughness.
-
5. Technical Benefits
-
Extended Component Life: By avoiding mechanical damage and excessive heat, FeatherPulse preserves substrate metallurgy and prolongs service intervals.
-
High Throughput: Up to 800 mm³/min on FP‑1000r cells means entire blade sets can be cleaned in under an hour.
-
Versatility: One laser head handles a range of tasks—from deep‑scale removal on hot‑section parts to fine‑film stripping on composite fairings.
-
Reduced Fixturing Complexity: Fiber‑delivered beam and small‐spot galvo optics access narrow ribs and platform slots without complex tooling.
-
Repeatable Quality: Digital recipe storage ensures identical results across shifts and facilities, simplifying certification and audit trails.
FeatherPulse Laser Ablation delivers the ultimate balance of power, precision, and process intelligence—enabling aerospace MRO teams to clean, prepare, and refurbish critical components faster and safer than ever before.
High‑Pressure Turbine (HPT) Blades
Compressor & Fan Blades
-
Rolls‑Royce & University of Manchester: Research at Manchester’s Laser Processing Research Centre (2003–2013) led to automatic laser cleaning implementation for Ti alloys in compressor drums, achieving near‑100 % “first‑time right” welds and multi‑million‑pound annual savings by eliminating chemical baths [3](REF Impact Case Studies).
-
BAE Systems: Adopted the same process to replace chemical cleaning in airframe manufacture, further reducing waste and labor [4](Research Explorer).
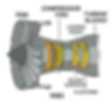
1. Principles of Laser Cleaning
Laser cleaning uses focused laser pulses to remove contaminants—such as soot, oxides, CMAS (CaO–MgO–Al₂O₃–SiO₂), and grease—from turbine engine components without abrasive media or chemicals. Key mechanisms include:
-
Photothermal/Photomechanical Ablation: High‑peak‑power pulses (10–100 ns) induce rapid thermal expansion and shockwaves, spalling off deposits while preserving the substrate [1](ScienceDirect).
-
Wavelength Selectivity: Near‑infrared (1064 nm) Nd:YAG fibers exploit stronger absorption by contaminants versus metal, maximizing cleaning efficiency [2](SSRN).
-
Assist Gases: Argon or nitrogen (1–5 bar) flows purge ablated debris and inhibit re‑oxidation during cleaning [1](ScienceDirect).
2. Research on Turbine Blade Cleaning
2.1 High‑Pressure Turbine (HPT) Blades
Studies on nickel‑based superalloy blades coated with Y₂O₃‑stabilized ZrO₂ show that continuous‑wave fiber lasers (power density ≈ 7.96 × 10^6 W/cm²) effectively remove CMAS deposits under argon, delivering clean surfaces with controlled roughness [1](ScienceDirect). Integration of pulsed and continuous modes further improves oxide removal quality and throughput [2](SSRN).
2.2 Compressor & Fan Blades
Surface fouling on compressor stages degrades aerodynamics; laser ablation can strip oxide scales and debris without altering blade geometry. Early work demonstrated no microstructural damage when parameters are optimized, confirmed via SEM and X‑ray analyses [6](kones.eu).
Precision Efficiency
SPARCL.AI Benefits for Turbofan Assembly Cleaning
-
AI‑Optimized Cleaning Recipes
Automatically generate laser parameters (pulse energy, repetition rate, scan speed) tailored to each turbofan component—fan blades, compressor stages, turbine vanes—to ensure “right‑first‑time” contaminant removal. -
Vision‑Guided Robotics
3D scanners map complex geometries (ribs, platforms, cooling channels), while SPARCL.AI’s path‑planning engine programs collision‑free, high‑efficiency scan patterns for complete, uniform coverage. -
Minimal Heat‑Affected Zone
Real‑time feedback control keeps HAZ under 100 µm, preserving substrate microstructure in nickel superalloys, titanium alloys, and thermal‑barrier coatings. -
Multi‑Pass Contaminant Strategy
Layered cleaning approach—low‑power pass for sealants and oils, high‑power pass for oxides and CMAS, finish pass for surface “polish”—maximizes throughput and surface integrity. -
High Throughput & Scalability
Gemini Robotics 2.0 cells with dual 500–1,000 W lasers achieve up to 800 mm³/min per arm, enabling full turbofan blade‑set cleaning in under an hour. -
Dry, Chemical‑Free Process
Laser ablation vaporizes deposits—no solvents, acids, or blast media—eliminating wash racks, wastewater treatment, and chemical handling protocols. -
Integrated Quality Assurance
Inline laser profilometry and borescope inspection verify removal depth, surface roughness, and coating integrity; automated pass/fail reports streamline FAA and OEM audits. -
Reduced Fixture Complexity
Fiber‑delivered beam and small‑spot galvos access narrow inter‑blade channels without custom tooling, shortening setup times and increasing cell utilization. -
Digital Traceability & Reporting
Comprehensive process logs—including part IDs, parameter sets, sensor data, and images—ensure full traceability for each cleaned component. -
Adaptive Learning Loop
SPARCL.AI continuously refines cleaning recipes based on live results, improving efficiency and consistency across different turbofan models and contaminant profiles.